Fuel Filtration & Tank Cleaning
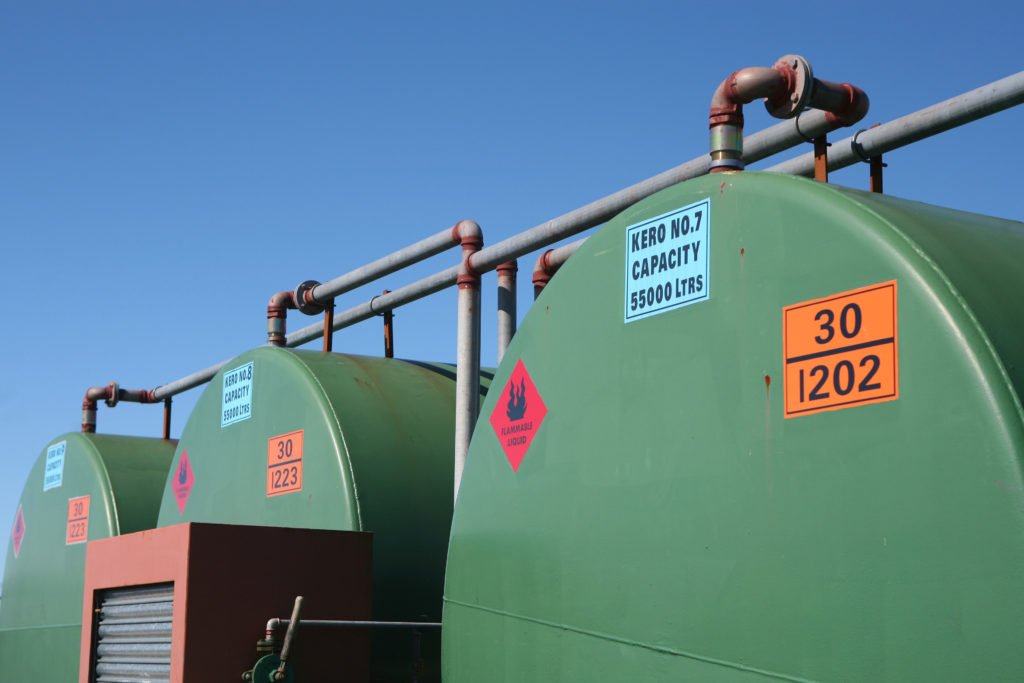
Many facilities have Emergency Power Systems (EPS), or back up generators, on site. Although systems are tested periodically, they very seldom run for an extended period under full load. When started, the contents in the fuel storage tank are agitated and suspended. If water and contaminants have collected in the fuel storage tank, the filters on the diesel engines may be overwhelmed, and the EPS will fail due to fuel starvation caused by clogged filters.
Most Emergency Power Systems failures are caused by foreign matter in the tank. To avoid this problem, fuel storage tanks should be routinely inspected and cleaned when necessary. A good preventative maintenance program should be in place to insure clean, reliable fuel.
All tanks are vented to the atmosphere; therefore, the fuel is subjected to airborne organisms and particles. Moisture from the air causes condensation on the inside tank walls. Another source of water is rain. Defective gaskets, broken caps and uncovered vents will allow water to accumulate in a tank. Because water is heavier than oil, water droplets will bind together and make their way to the bottom of the tank. Once at the bottom the water is trapped.
Microorganisms will begin to grow in the water and feed off of the fuel. Over time, the interface layer between the fuel and water will become a stringy, black mass. Sediments will form on the tank bottom as the organisms go through life processes. The pH level of the water will lower causing the water to become corrosive.
Fuel also goes through a natural process of degradation called repolymerization. In this process, microscopic particle will link together to form agglomerates (macroscopic sludge). The fuel may become too dirty to be pumped and non-combustible. The layers of sludge and water settle to the bottom of a tank where the fuel pick-up line is located. That is why the NFPA recommends steps be taken to maintain fuel integrity (NFPA 110, 7.9.1.3).
To clean a tank, the bottom layers of sludge and water, as well as the interface layer, should be removed first. To do so, the entire bottom of a tank must be accessed. Once that process is completed, the fuel, then, must be agitated to suspend any remaining contaminants so they can be filtered out.
Fuel filtration is essential for back up systems that do not regularly turn over their fuel. 90% of generator problems are fuel related. Fuel filtration will ensure a clean, reliable fuel source, protect the tank from corrosion and extend the life of the equipment that the fuel and tank support. Below are considerations for the establishment of a good preventive maintenance program for your EPS:
-
Sampling: Sampling should be done at least once a year. Samples should be drawn off the bottom to about 10″. This is the typical location of the fuel pick up where problems are mostly likely to occur.
-
Lab analysis: Sampling will provide a visual inspection of the fuel. This will indicate if there are any obvious problems. Further analysis will have to be done in a lab. For a complete diesel analysis, test for: water, sediment, flash point, particulate contamination, microbiological growth, acid number, corrosion, cetane index and storage ability. These tests are geared specifically for diesel fuel. Unless the sample is drawn from the interface layer at the bottom, the results may be misleading.
-
How often should a tank be cleaned? This depends on location and how critical the system is deemed. The NFPA mandates that fresh fuel be on hand. Yearly monitoring will indicate when cleaning is required. A good rule of thumb for critical systems is every 2 to 3 years. Non-critical systems should be cleaned every 3 to 5 years.
-
Tank Cleaning: The best way to clean a tank is to drain it, wipe down the inside of the tank with a squeegee, dispose of the contaminants and filter the fuel back in. Not only may this be impractical and expensive, but also it may be impossible for small hard-to-access tanks. Fuel filtration can achieve the same goals without setting up a second energy source.
When employing a fuel filtration service be sure to consider the following
-
Can the entire bottom of the tank be accessed? This can only be accomplished by the use of flexible wands that can be dragged and pushed along the bottom similar to vacuuming the bottom of a pool. Don’t expect contaminants to come to a stationary point.
-
What micron size is being used in filtration? Removal of all the microorganisms requires using a 0.5-micron filter.
-
Does the filtration system being used have an in-line oil-water separator? Bulk water can be pumped straight off a tank, but emulsified, or suspended water, must be mechanically separated.
-
Does the filtration system being used have in-line water absorption filters? Water absorption filters strip out any emulsified water that is missed by oil-water separators. These filters bring the water content to below 100 ppm/ml well below the industry standard of 500 ppm/ml.
-
Does your contractor treat the tank chemically? After cleaning a tank, it should be treated with an inhibitor to stabilize the fuel for storage. The use of chemicals can prolong the cleaning cycle. A multipurpose inhibitor that contains a detergent, a dispersant, a biocide, a demulsifier, a corrosion-inhibitor, a metal deactivator and a polymerization retardant should be used. Fuel does not come with these ingredients; thus, they need to be added.
Diesel fuel is considered a middle distillate. It has a shelf life of approximately 1 and 1/2 to 2 years. It is an organic compound and is affected by the presence of air, water and microbiological growth. Whether you are backing up life support equipment, telecommunications, computers, fire pumps, sewer stations or any other diesel generated electricity, a preventative maintenance and monitoring program will allow for the perpetual storage of fuel for emergency situations.
Need your tank cleaned?
Give us a call today for a free quote!